Material and Settings
There are many options to close from for material, and the SoarKraft models are designed to work with just about any type of material to make a flyable model. Some materials are stronger, some are lighter, and more and more come out all the time. You do not need to settle on one material, you can mix and match to suit your flying conditions or performance level. Some specific "slicer" setting are necessary, but hopefully the following will help with that. Also see our Youtube channels for new materials. Use whatever you want.
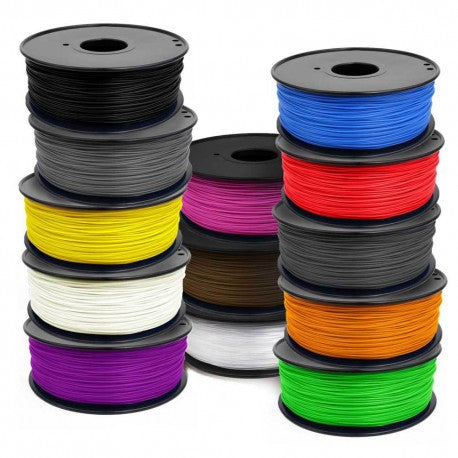
Easy Materials
SoarKraft designs can be printed in many different materials, but do not require anything special other than proper settings. Printing thin wall sections will take special settings, and test prints are recommended. Start with a tail fin or the SoarKraft test print.
PLA - Easy - cheap - stiff - great for slope
PLA+ (PLAPro) - Easy - Best tough material.. better than PETG.
PETG - retraction setting are key - great colors - better for hot weather / sun - strong but flexible.
Foaming Light Weight PLA - increased printed difficulty - able to get 50% weight reduction but has variable density - flexible / feels like foam - expensive per roll / but makes 2x when printing.
Low Density PLA - light weight already (~65%) - prints with similar settings and ease of PLA - strong but flexible - new
Orca / Bambu / Prusa Slicer configuration settings below
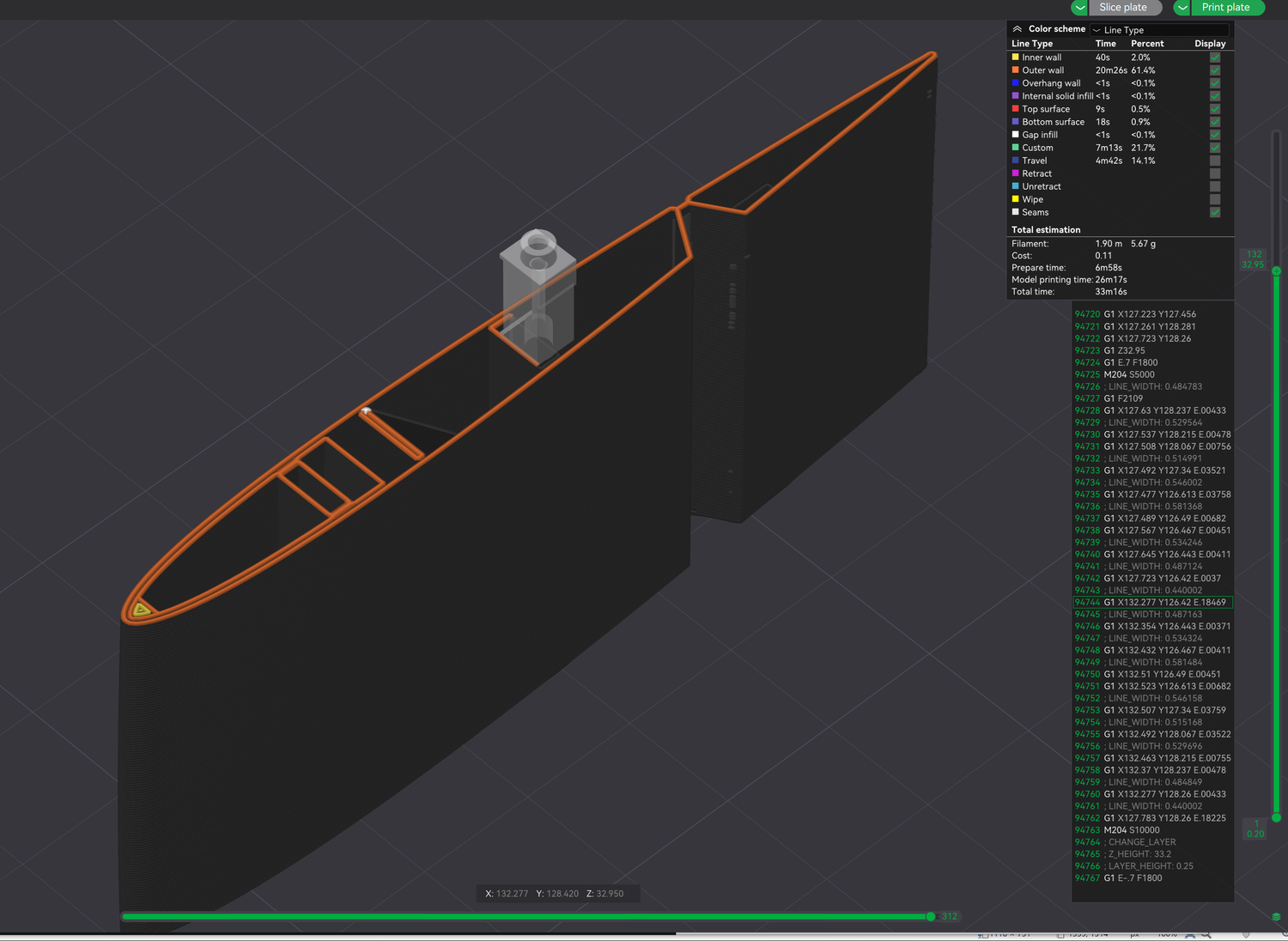
SoarKraft Test Part
Here is an example part use to set up your slicer and your printer. If you can print this part you should be able to print any of our models. This is v3 with the "Perimeter before Inner" design.
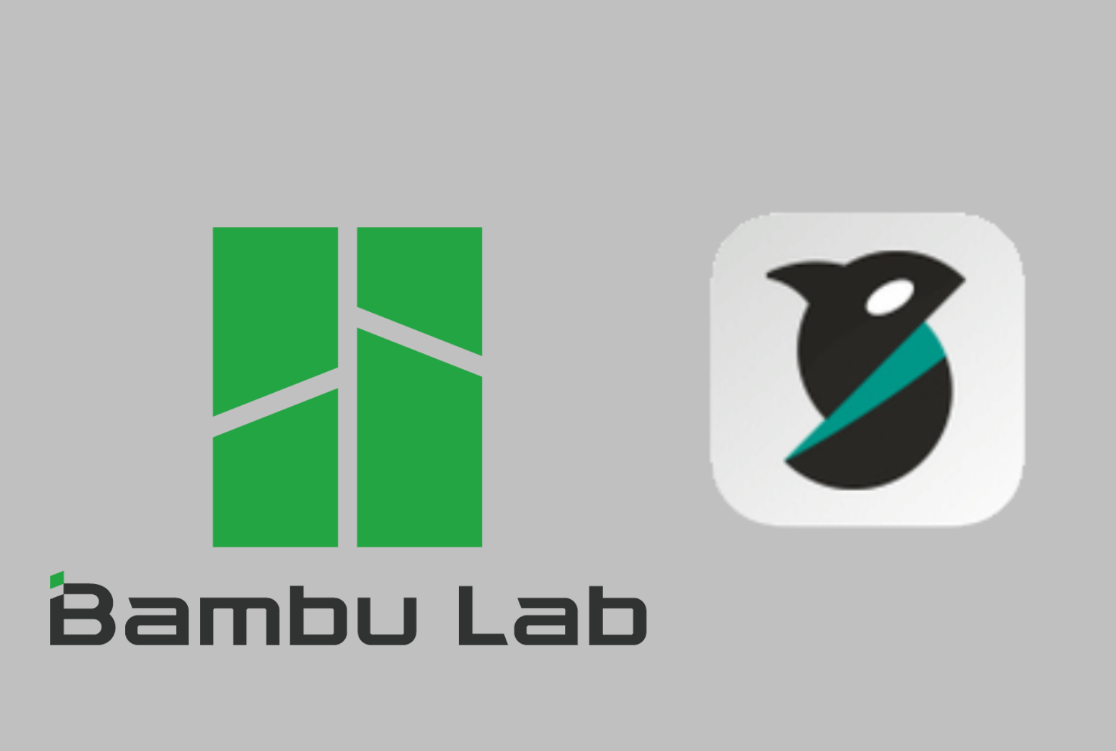
PLA - Bambu / Orca
Configuration files for PLA - Download and "Import Config" these .json files for Bambu Studio or Orca Slicer. These are for Generic PLA - Process and Filament. For PLA Pro / PLA+ increase nozzle temp to 220... Works for Polymaker HT-PLA too
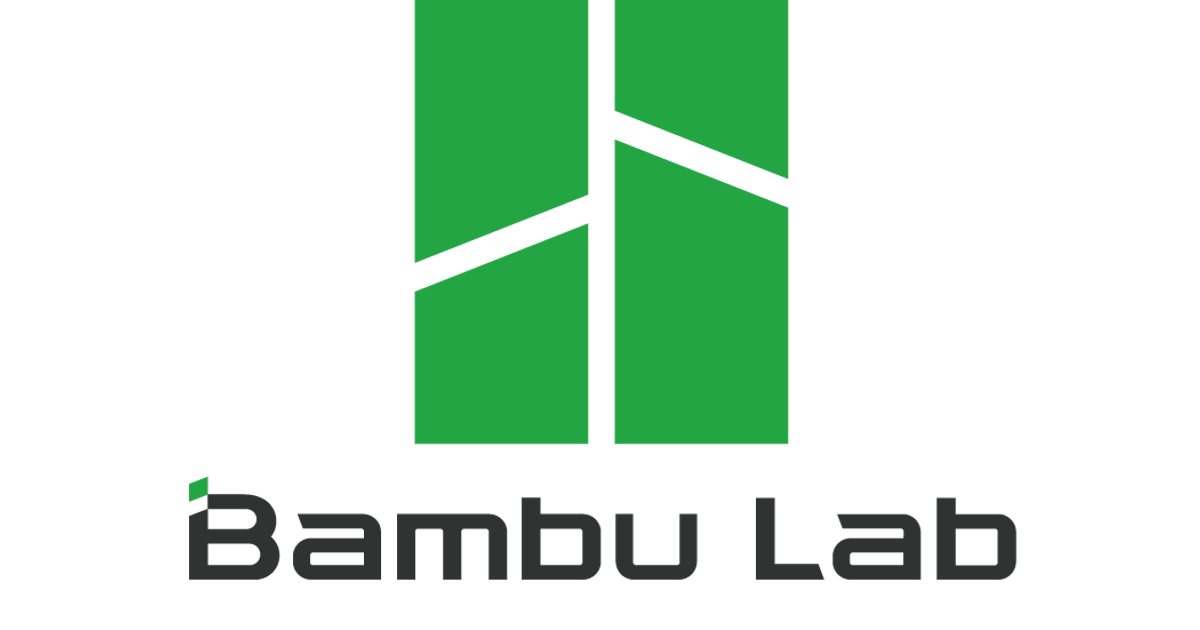
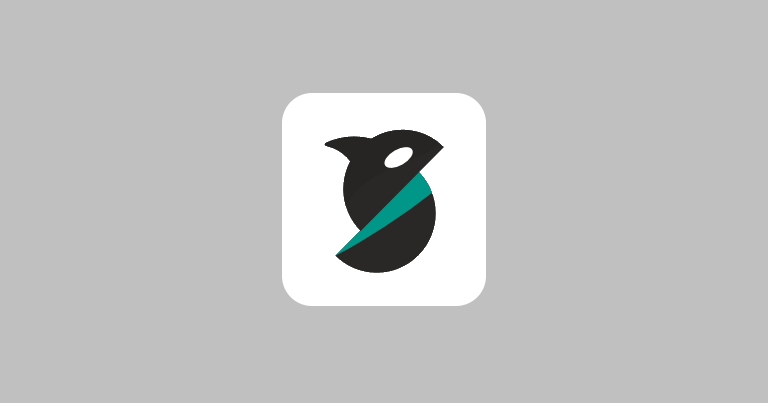
LIGHT WEIGHT LW-PLA
Config Files for Bambu / ORCA to Import - for X1C and P1S

ColorFabb foaming LW-PLA-HT
Config Files for Bambu / Orca to Import for Bambu X1C and P1S. This is a foaming material that can handle higher environment temperatures after printing.

ASA - Config (NEW)
This is the config for Bambu/Orca for the X1C and P1S, process and filament .json files for any ASA filament, but tested on Polymaker ASA. These will import into Bambu Studio or Orca Slicer for ether an X1C .4mm nozzle or P1S .4mm nozzle and show up in User Presets. If ytou have a different printer sellected it will not show up. Use the settings transfer method in my "Orca Slicer - Use and Printer" video on my youtube channel (link on this page)
these are the setting used in my ASA / HT-PLA comparison video. Used with smooth PEI Plate and glue stick. Recommend closed printer for print quality and smell containment.
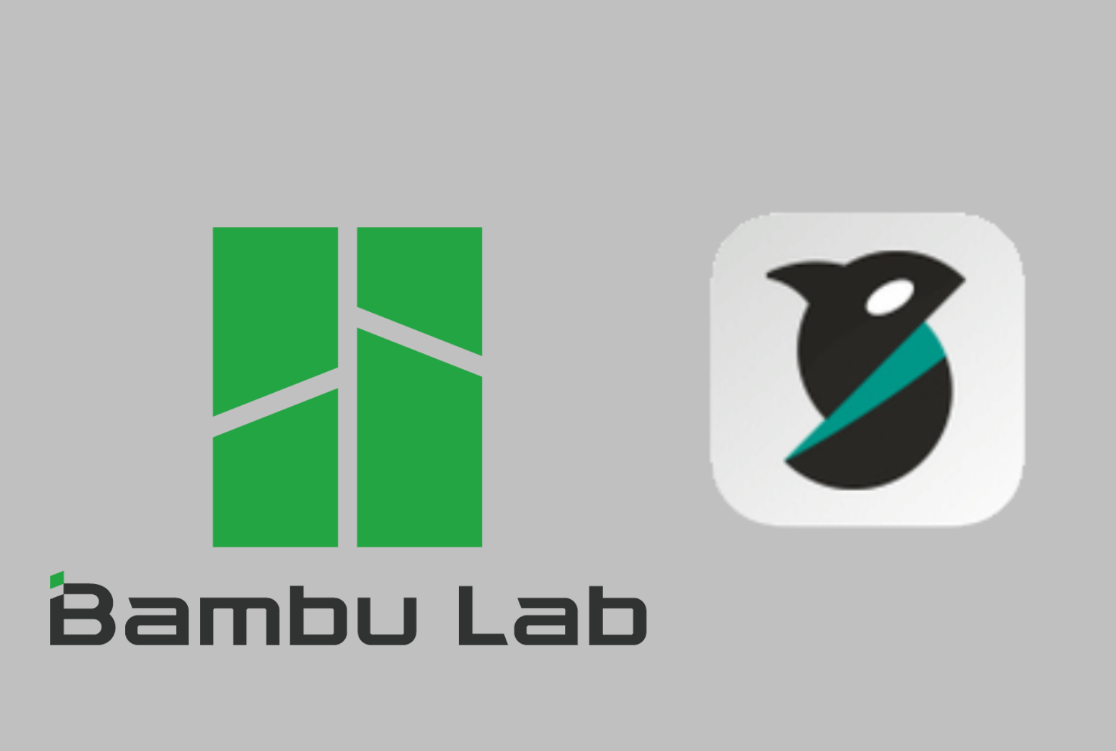
Hyper PLA
Filament and Process Configuration for import into Bambu Studio or Orca Slicer at 27mm^3/sec and 5000mm/s^2
As used in review video
For X1C and P1S
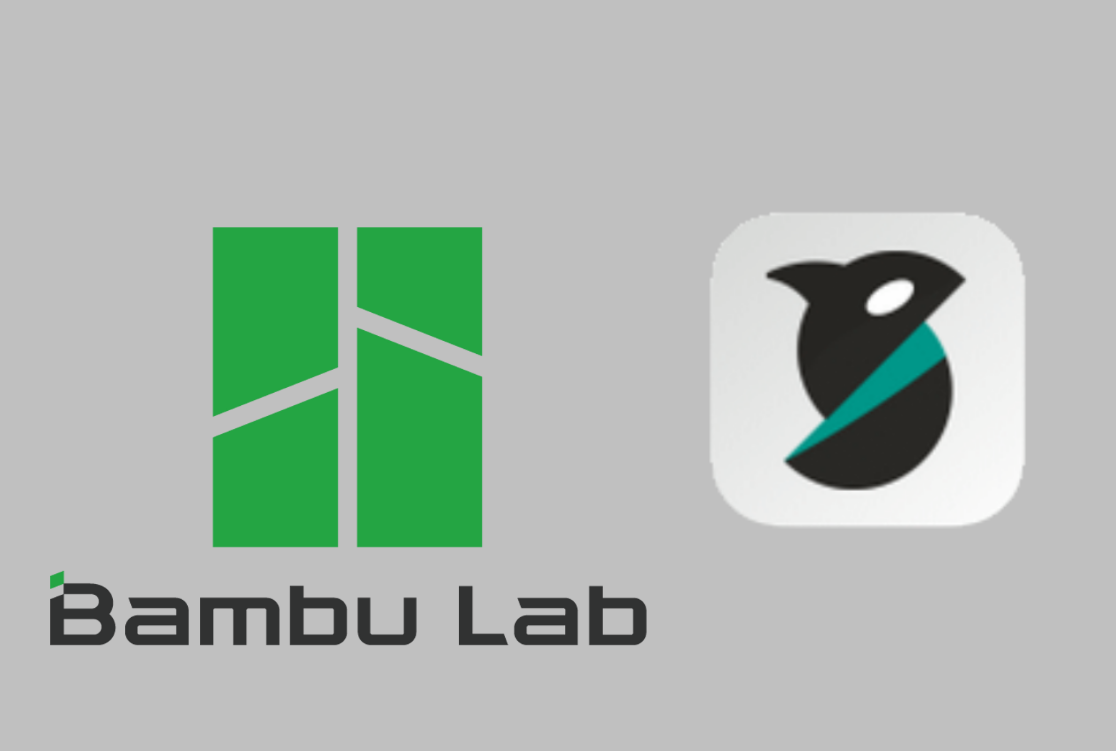
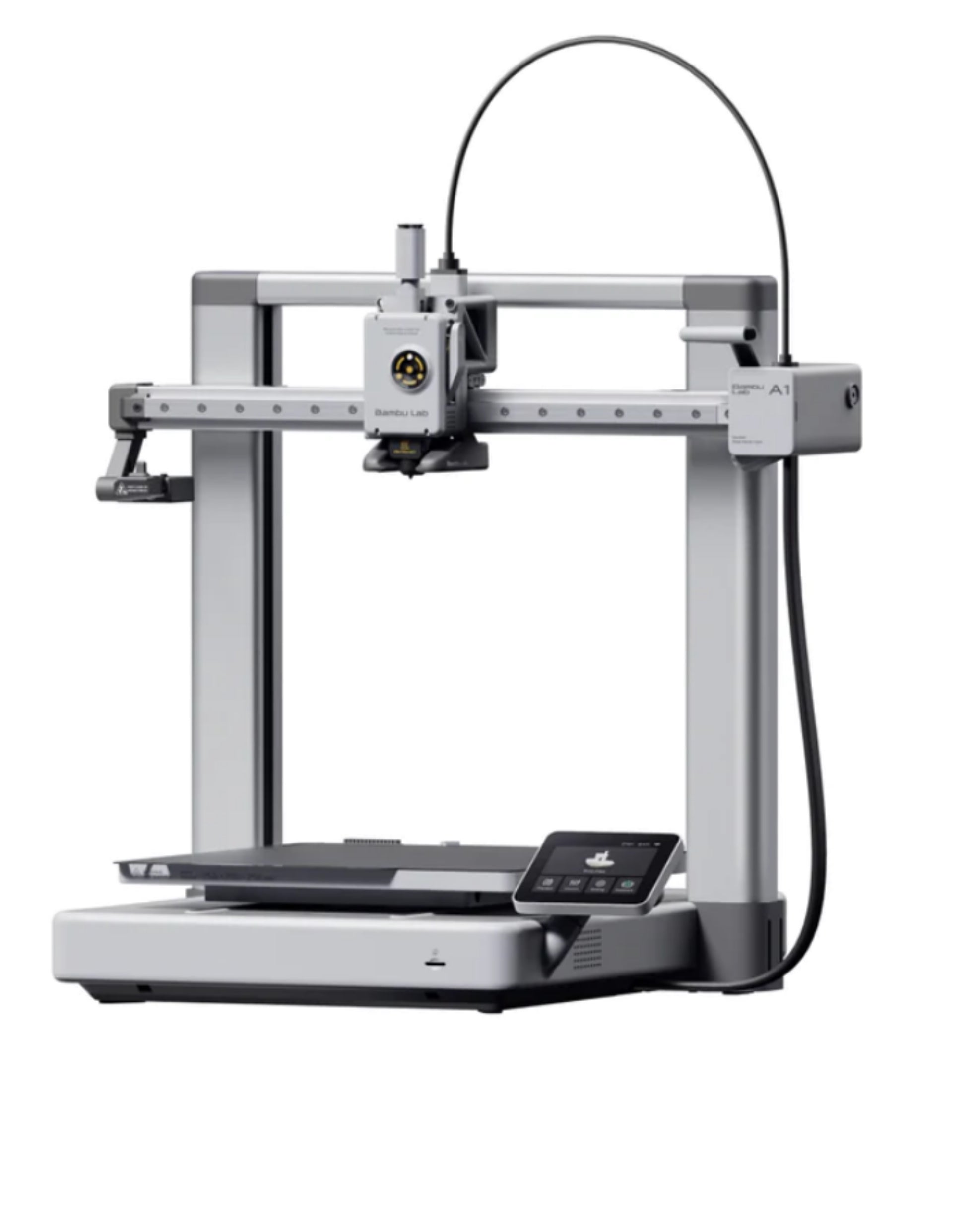
New Bambu A1 (Big)
BS and Orca Slicer A1 Process and Filament .JSON files
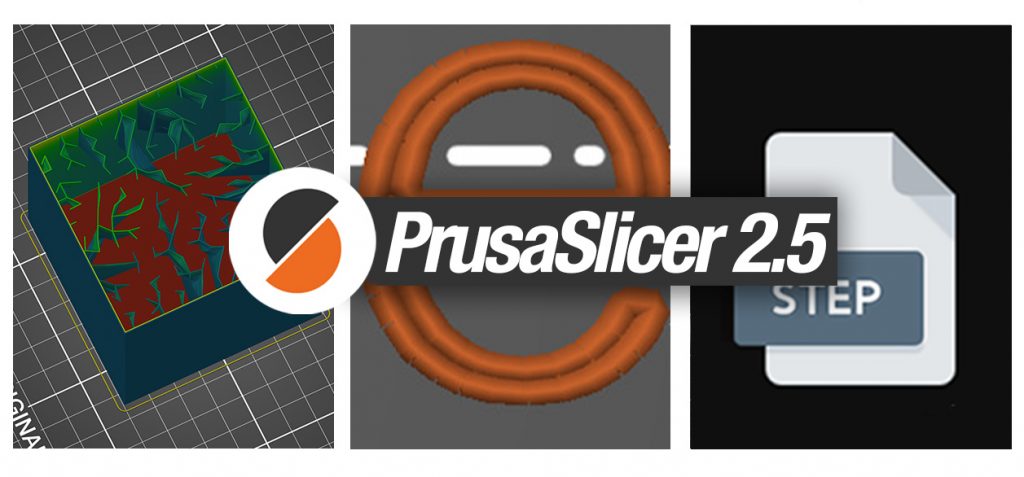
Basic PrusaSlicer Profiles
Download and import the .ini configuration file for PLA, LW-PLA, and a test part. Get started printing - more material configurations coming soon.

Cura Settings - No Longer Supported
New file sets don't work well with any version of Cura... Use Prusa Slicer, its way better. Here are old setting reference for some of the materials for the Cura Slicer. Cura 4.11-4.13 had the best results. Cura 5.0+ wokrs, but the Combing mode does not work properly.... nor does "outer before inner".... sure they will fix this?, but as of 5.5 it is still not working. Not waiting.
PLA+ - increase nozzle temp to 220

Bed Adhesion
On the older printers we print most all of our material on blue painters tape, Scotch Blue #2090. Because warping is a huge problem, any lifting can ruin a part. With a bed temperature of 60C for PLA and 85C for PETG, we get great parts every time... they are hard to get off... but a little rubbing alcohol and some heat (warm the print bed to 60C if cool) and tape gives way releasing the part. Brims are recommended if you are having trouble, but not necessary. The "skirt" tacks down the tape to help it stay in place while printing the first layer.... then it is good from there.
On the Bambu X1C we print on the "Cold Plate" with Glue Slick.
Best Slicer??
A bit outdated as these slicers are changing so fast, but still has good tips and information
Cura, PrusaSlicer and Simplify3D seam to be the most popular for preparing parts for 3D printing. However there are some new options - Specifically Bambu Studio / Orca Slicer.
We are always looking for better ways. A slicer is required and is an important part of 3D printing to know how to use. There are too many printers, materials and conditions that need to be part of the gcode, the specific machine instructions, to get a usable part... it is not hard and there are many resources to help understand what to do.